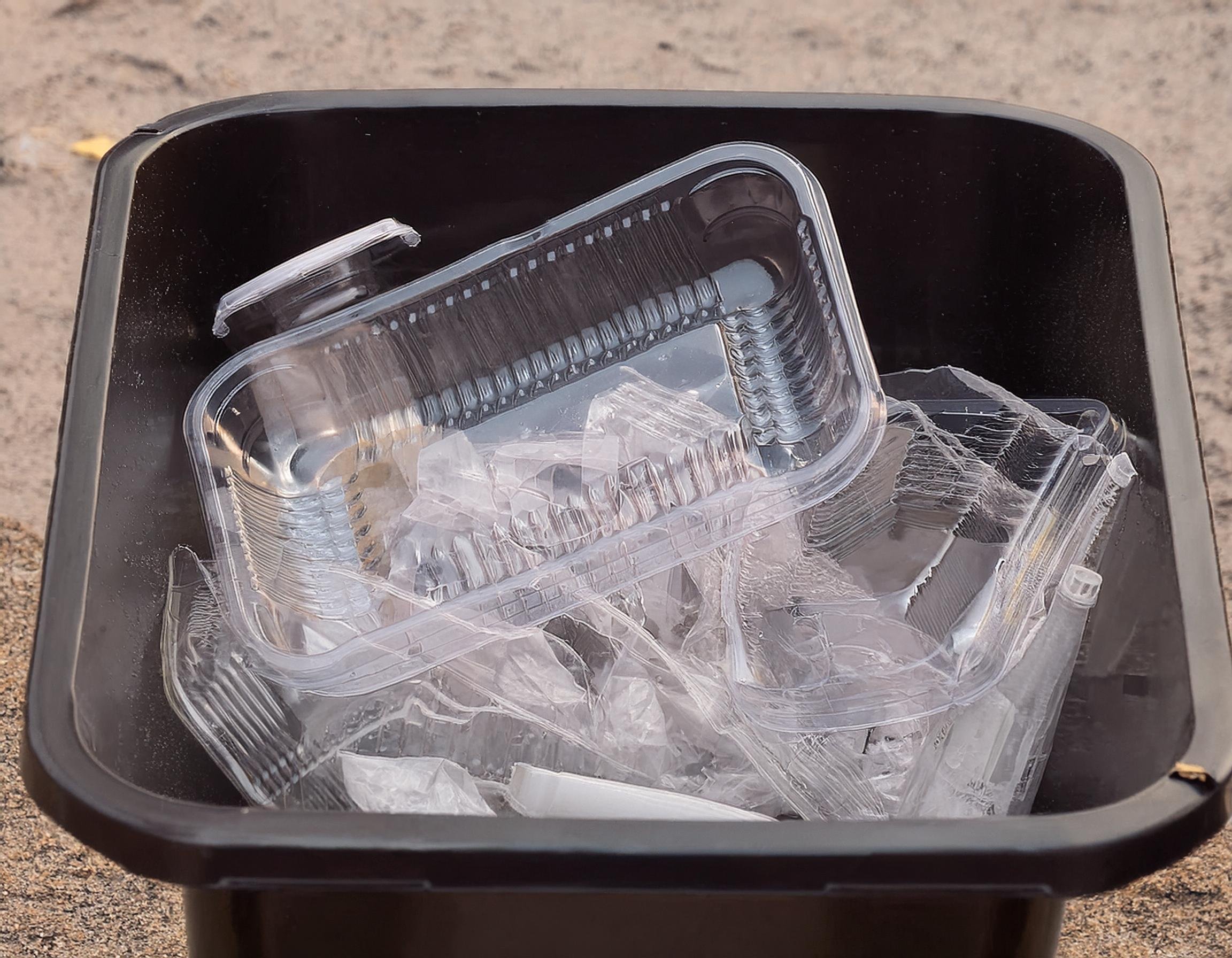
FREQUENTLY ASKED QUESTIONS
Chemical recycling (sometimes also called molecular recycling) refers to a suite of technologies including chemical, thermal, catalytic, bio/enzymatic, or other molecular processes to break down used plastics into their basic chemical building blocks. Chemical recycling offers the potential to complement traditional, mechanical recycling by providing a pathway toward circularity for mixed plastics, for complex/multi-material packaging formats such as flexible film and bags (HDPE #2 or LDPE #4), and for resins such as polypropylene (#5) and polystyrene (#6) which are not widely recycled mechanically.
Mechanical recycling is the more widely known form of recycling in which used plastics are collected, sorted and separated by type, shredded, washed, and then put through an extrusion process to generate pellets. Those pellets are then sold to companies that use them either alone or mixed with traditional polymers to create new plastic articles. The types of plastic resins that are most widely recycled are PET (#1), used in beverage and soda bottles, and HDPE (#2), used in milk jugs and detergent containers.
Chemical recycling also uses source-separated plastic feedstock or the non-recyclable fraction from mechanical recycling systems. However, rather than extruding them to create pellets, a more intense process is used to change the essential chemical makeup of the plastic. The process includes applying heat, solvent, or other intervention to convert, break, or dissolve the plastic back into its original building block components, either as a liquid or gas. In many cases, a wider range of plastic resin, including many types of packaging, cannot be recycled in current systems and can often be processed using chemical recycling (such as flexible film packaging, chip bags, candy wrappers, pouches, industrial pallet wrap, and more). These materials can then be sold into a variety of production processes, including creating new plastic.
Although there are several new and promising technologies, chemical recycling technologies currently fall generally within one of three primary process categories:
Dissolution (Purification): Dissolution processes use a solvent and low heat to extract color or additives from a single-polymer feedstock, or target polymers from mixed plastic materials. Dissolution techniques do not change the polymer structure of the target plastics, using physical (i.e., mechanical) recycling technologies but with the addition of chemical solvents.
Depolymerization: Depolymerization processes take a single-resin feedstock and partially or fully break the polymer bonds using a solvent to generate monomers or oligomers. There are also several sub-categories, depending on whether the depolymerization process is primarily thermal, chemical, or a mixture of the two.
Conversion: Conversion technologies are the most studied chemical recycling techniques. These processes typically involve the thermal breakdown of the waste plastics in an oxygen-starved and combustion-free reactor, maintaining carbon in the final products of the conversion reaction (char, liquid oil, light gases and syngas) rather than releasing carbon as carbon-dioxide. These processes can also include catalytic steps to convert the liquid oil and syngas to select chemical products.
These chemical recycling technologies produce different outputs, ranging from chemicals and monomers, to waxes, syngas, and mixed hydrocarbons, as shown in this chart:
The outputs of mechanical and chemical recycling processes vary based on both the type of input (e.g., the particular plastic resin or mixture of resins) and the technology applied.
Mechanical recycling: Plastics put through this process are chipped, heated and reformed, but they never lose their essential chemical character as a polymer. The pellets which result from mechanical recycling are useful in a wide variety of applications, depending on their quality, grade, and the original material, and can be made into new consumer, packaging or industry products. Over time, some of the physical properties of the original plastics can degrade when subjected to repeated mechanical recycling.
Chemical recycling: Through these processes, the polymer bonds in used plastics are broken, creating completely different chemical structures such as gas and liquid hydrocarbons, which can be further processed into the basic chemical building blocks for plastic, known as monomers, or oligomers. The range of new plastic products created through this method are of “like-new” quality and can even be food grade.
The chart below illustrates the wide range of plastic resin types that can be accommodated within various technologies to produce a range of different products.
Whether chemical recycling should be considered “recycling” under various laws or the waste management hierarchy is a subject of sometimes intense debate. This is in part because using chemical recycling to process waste plastic can produce a wide range of outputs, with uses ranging from building blocks for new polymers, chemicals, waxes and lubricants, or even fuels.
Perhaps the most important point is that both mechanical and chemical recycling help society achieve greater circularity by making new products without the use of new virgin carbon as feedstock. Additionally, the outputs of both processes recover used plastic in order to avoid disposal through less desirable landfilling or combustion pathways.
We posit that the fractions of chemical recycling outputs that are transparently traced and used to produce new polymer, chemical or other non-polymer products should be thought of as “recycled” because they offset the use of virgin feedstock. However, outputs which are used to produce a fuel are more properly described as “recovered” since it is the energy value that is recovered for a one-way use as a fuel.
In any event, it is important to understand that all production from chemical recycling – whether under “recovered” or “recycled” – is a complement to other forms of recycling and provides a beneficial outcome by reducing use of virgin feedstock and avoiding either combustion or landfill disposal.
Source: Responsible Production Guidelines Consortium. (2024, May). Responsible production guidelines to ensure progressive advanced / chemical / molecular recycling operations.
Source: Responsible Production Guidelines Consortium. (2024, May). Responsible production guidelines to ensure progressive advanced / chemical / molecular recycling operations.
No, chemical recycling and combustion/incineration are entirely different processes, each with different and distinct outputs and emission profiles. While both processes use high heat and are used to reduce the amount of waste disposed in a landfill (including hazardous waste and non-recyclable waste), they differ in almost every other aspect.
Combustion/Incineration EPA describes the combustion of non-hazardous waste (e.g., Municipal Solid Waste) as a form of energy recovery, along with technologies that convert non-recyclable waste materials into usable forms of energy including heat, electricity, or fuel through a variety of processes, including combustion, gasification, pyrolization and anaerobic digestion, and landfill gas recovery. (See: Energy Recovery from the Combustion of Municipal Solid Waste (MSW) | US EPA)
Pyrolysis is a closed, oxygen-free process in which plastic waste is subjected to extremely high temperatures (400°C to 1000°C). It differs from combustion/incineration because there is no oxygen involved. The pyrolysis process includes both energy and “resource” or “feedstock” recovery by creating gas or liquid raw materials, which can be used to make new products, offering greater circularity potential.
Combustion processes are distinct from pyrolysis because they include oxygen, the combustion of which can generate hazardous air pollutants and particulate matter. However, the EPA requires that an incinerator destroy and remove “at least 99.99% of each harmful chemical in the waste it processes.” Additionally, the heat used in the incineration process can generate electric energy, which is known as the “waste to energy” process.
While this discussion focuses on pyrolysis—because it is the most publicly debated and frequently conflated with incineration—we recognize that advanced recycling encompasses a broader suite of technologies, including gasification, depolymerization, solvolysis, enzymatic hydrolysis, and others.
Each of these processes has its own technical profile, environmental footprint, and material recovery potential, and should be evaluated independently using science-based, data-driven assessments
Learn more:
Incineration: Energy Recovery from the Combustion of Municipal Solid Waste (MSW) | US EPA
Life Cycle Assessments (LCAs) are a widely used tool that utilizes comprehensive, transparent, and science-based approaches to help evaluate potential environmental impacts of goods and services. LCAs have recently been used to evaluate chemical recycling technologies, including pyrolysis, depolymerization, and dissolution.
Understanding LCA results requires context. When conducting LCAs – and when evaluating their results – it is important to transparently set forth the goal, scope, system boundary, functional unit, and allocation approaches regarding choices and assumptions used in modeling to ensure reliable results and to support consistent comparisons. It is also important to understand any inherent limitations and uncertainties, as they can influence results and their interpretation.
An example of the importance of context is in the evaluation of “avoided emissions” from chemical recycling. In these cases, the phrase “avoided emissions” refers to greenhouse gas reductions that occur when these processes displace more carbon-intensive alternatives, such as virgin plastic production, landfill disposal, or incineration. Including avoided emissions, or other avoided impacts, can add valuable context and insights to an LCA in understanding the net environmental benefits of chemical recycling. However, any avoided impacts must be applied transparently, with clearly defined assumptions, methodological rigor, and well-established baseline scenarios and system boundaries to avoid miscommunication. Full-system comparisons are essential to prevent misleading conclusions, as key factors such as conversion rates, energy and process efficiency, end market substitutions, and regulatory and market dynamics can influence overall calculated avoided emissions.
While they can help inform decision-making, LCAs are generally not suitable as the sole determinant for financial decisions, policymaking, or substantiating sustainability.